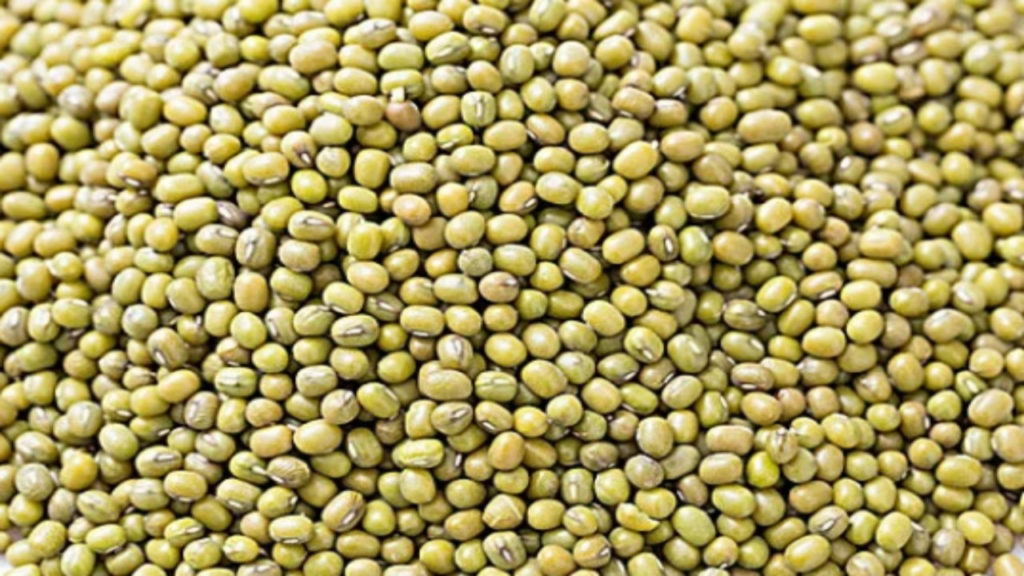
Magnetic Separators: In food processing, efficiency is key to meeting high demand, reducing operational costs, and maintaining consistent product quality. To ensure that production runs smoothly and products remain safe, manufacturers must address various challenges, one of the most critical being metal contamination. Magnetic separators have become an indispensable tool in food processing, improving both the efficiency and safety of operations. The process of magnetic separation involves using magnetic fields to attract and remove ferrous and non-ferrous metal contaminants from raw materials, intermediate products, and finished goods. By removing these contaminants, magnetic separators not only enhance quality control but also streamline production processes, minimize downtime, and safeguard equipment.
Metal Contamination Prevention
Metal contamination can occur in a variety of ways during food processing. It might come from machinery wear and tear, packaging materials, or even raw ingredients. Regardless of the source, metal particles in food products pose significant risks. They can damage equipment, cause product recalls, or even lead to consumer health issues. Magnetic separators play a pivotal role in addressing these risks by effectively removing ferrous and non-ferrous metal contaminants from ingredients and finished products. This process ensures that food products are not only safe to consume but also meet quality standards set by regulatory authorities.
Minimizing Equipment Damage and Downtime
Metal particles are not just a concern for food safety; they also pose a threat to processing equipment. As metal contaminants pass through machines like grinders, mixers, or conveyors, they can cause wear, tear, and even catastrophic failure of critical components. This leads to expensive repairs and significant downtime, ultimately affecting overall production efficiency. Magnetic separators help prevent this issue by removing metal contaminants before they reach sensitive machinery. By acting as a safeguard, magnetic separators help protect equipment from unnecessary damage, leading to fewer breakdowns, less maintenance, and reduced unplanned downtime. This protection translates to improved operational uptime and a more reliable production process.
Optimizing Production Efficiency
One of the primary benefits of magnetic separators is their ability to maintain a continuous, uninterrupted production flow. Without the need for constant manual inspections for metal contaminants, operators can focus on other critical tasks. Magnetic separators are automated, which means they remove contaminants in real-time, allowing the production process to run smoothly without delays. Additionally, because these systems reduce the need for manual cleaning and maintenance, they save on labor costs and contribute to more streamlined operations. This increased efficiency not only boosts overall productivity but also enhances throughput, ensuring that more products can be processed in less time.
Compliance with Food Safety Standards
In the food processing industry, compliance with stringent food safety regulations is non-negotiable. Standards such as those set by the FDA, HACCP, and ISO certifications require manufacturers to ensure their products are free from harmful contaminants. Magnetic separators are an essential tool in meeting these safety standards, as they help eliminate metal contamination that could lead to non-compliance. By incorporating magnetic separation systems into their operations, food manufacturers can confidently meet regulatory requirements, reduce the risk of costly fines or recalls, and maintain consumer trust.
Cost-Efficiency and Long-Term ROI
While there is an upfront cost associated with installing magnetic separators, the long-term financial benefits make them a worthwhile investment. The hidden costs of metal contamination—including product recalls, equipment repairs, and reputational damage—can quickly add up. Magnetic separators help mitigate these risks by ensuring that metal particles are removed before they can cause significant problems. Additionally, by protecting machinery and optimizing production processes, they reduce downtime and maintenance costs, leading to a solid return on investment (ROI). In the long run, magnetic separators contribute to a more cost-effective, efficient, and profitable food processing operation.
Conclusion
Magnetic separators play a crucial role in improving the efficiency of food processing operations. By preventing metal contamination, protecting valuable equipment, optimizing production flows, and ensuring compliance with safety regulations, these systems enhance both the safety and productivity of the manufacturing process. Their ability to reduce downtime, minimize maintenance costs, and protect against contamination-related financial risks makes them a valuable investment for any food manufacturer looking to improve operational efficiency and ensure high-quality products.